NESTING ИЛИ РАСКРОЙ: МУКИ ВЫБОРА
Обзоры
19.01.2024
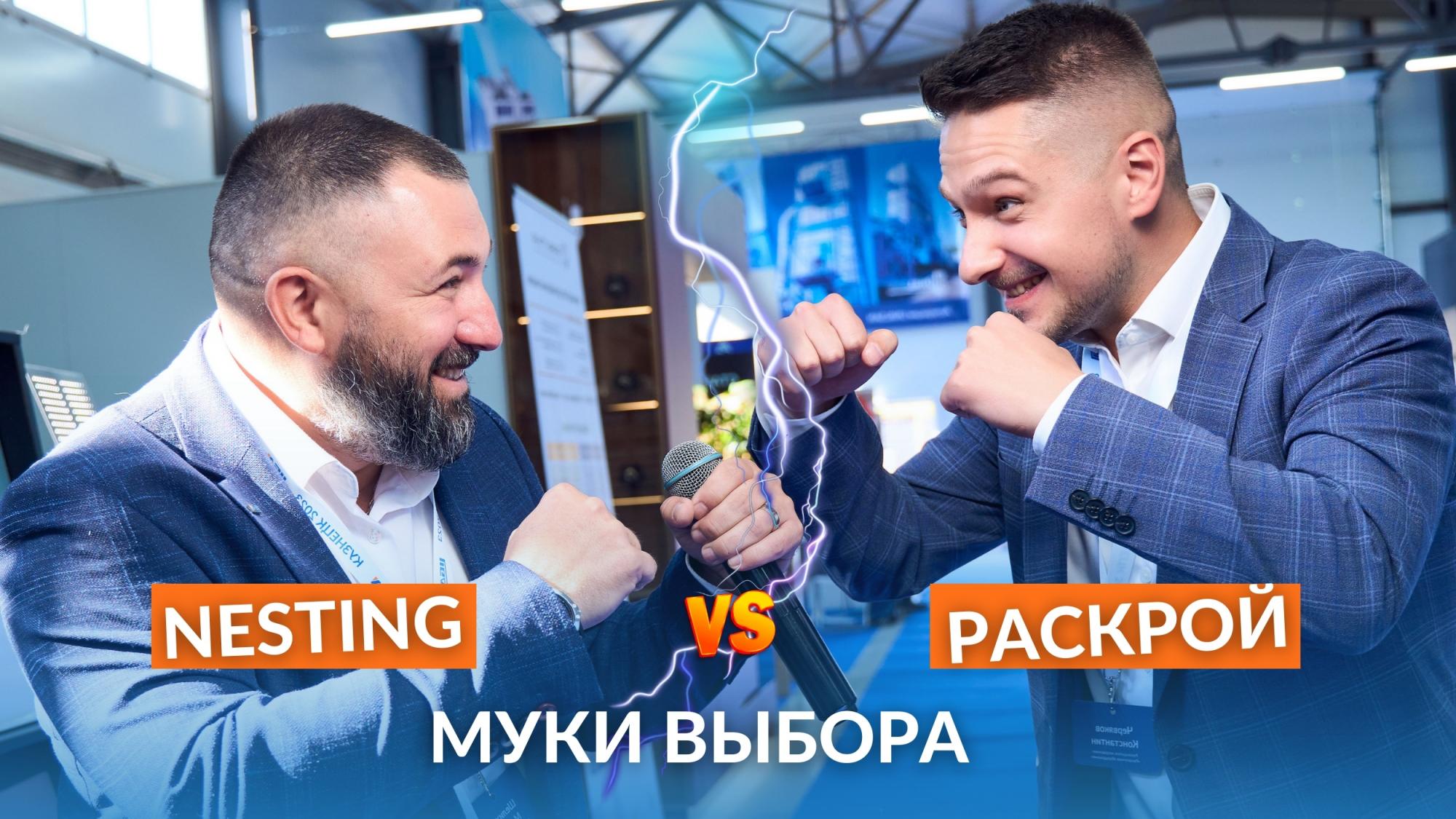
Форматно–раскроечный станок перестал быть «альфой» мебельного производства. Ему на смену пришли пильные центры и обрабатывающие центры с ЧПУ. Будущее уже наступило и скоро пройдет мимо, а мебельщики все еще сомневаются, что выбрать: нестинг или классический раскрой? Как сделать правильный выбор? Отринем эмоции, посмотрим на это эпическое противостояние с цифрами в руках, приведем аргументы обеих сторон и послушаем отзывы реальных мебельных производств.
Уровень технического оснащения отечественного мебельного рынка год от года растет. Автоматические кромочники вытесняют своих ручных и полуавтоматических собратьев, а сверлильно-присадочные центры с ЧПУ встают на место одношпиндельных станков. Но чтобы непрерывно снабжать деталями какой-нибудь трехголовый присадочник одной форматки уже явно недостаточно.
И здесь мебельщики встают перед выбором, которого в предыдущих случаях не было. Теперь у них есть два типа оборудования: пильные центры с ЧПУ и обрабатывающие центры с ЧПУ. И тот, и другой вариант уменьшают влияние человеческого фактора, в разы повышают КПД участка раскроя, экономят фонд оплаты труда и т. п. Понятно, что крупные серии по зубам только пильным центрам, но что выбрать для индивидуального или мелкосерийного производства, когда пилят по одному листу? Есть ли однозначный ответ, за какой технологией будущее?
Концептуально, форматно-раскроечный центр — это форматка «на максималках». Но по конструкции — это станки–антагонисты. В работе на форматке очень многое зависит от оператора, который надвигает заготовку на стационарный пильный узел. Даже если оставить за скобками точность размеров, выставляемых по линзе («плюс-минус полмиллиметра — не брак»), у человека все равно остается масса возможностей криво распустить ЛДСП, особенно, если станок уже кое-где разболтался. В общем, хороший оператор форматки на вес золота.
Пильный центр, наоборот, крепко фиксирует лист прижимной балкой и надвигает на него пильный узел. В этой машине очень многим управляет компьютер: он оптимизирует карту раскроя, перемещает листы ЛДСП, следит за безопасностью человека, подсказывает ему, что делать, мониторит собственное состояние и даже самостоятельно подстраивает вылет пилы под толщину пакета ЛДСП. Боковые выравниватели и толкатели оставляют оператору очень немного свободы даже для того, чтобы неровно поставить заготовку. По существу, роль человека сводится к тому, чтобы поворачивать детали в нужном направлении и нажимать на кнопку запуска пилы.
Главный плюс пильного центра — он может за один раз распилить пачку из 5–7 листов. То есть, производительность этой машины на порядок выше, чем у форматно-раскроечного станка. Впрочем, даже распуская по одному листу, центр имеет перед ней солидное преимущество.
Константин Червяков «Многие говорят, — комментирует руководитель направления «Раскроечное оборудование» LIGA Константин Червяков, — что на форматке они могут использовать материал более оптимально. Они прямо в голове оптимизируют раскрой, а потом по 20 раз вращают лист, чтобы получить из него максимум. Что я могу на это сказать? Здорово, когда есть столько свободного времени, но пока вы будете вращать детали, убирать и класть новые, то убьете полчаса на лист, который центр раскроит за 5–6 минут. Одно дело, когда нужно напилить 20 плит в месяц, и совсем другое, когда речь идет о 80–90 листах за 12–часовую смену. Пильные центры используют и те фабрики, которые оказывают услуги коммерческого раскроя. Хотя каждый заказ — это разные карты, которые можно было бы бросать на нестинговую машину, но фабрики предпочитают использовать классические форматно-раскроечные центры. Во всяком случае, за 10 лет работы я встретил только одно производство, которое делает коммерческий раскрой на нестинге. |
![]() |
В значительной мере эта ситуация связана с себестоимостью услуги. Фабрики–конкуренты борются друг с другом за каждую копейку и стараются минимизировать все расходы».
Концепция нестинга включает в себя программную и техническую части. Программная отвечает за максимально эффективное размещение деталей на листе, чтобы минимизировать отходы и сократить время раскроя и, заодно, присадить отверстия в пласть. Техническая часть включает в себя обрабатывающий центр с ЧПУ, который должен все это сделать сам и исключить из процесса оператора. Тому остается только контролировать, все ли идет по плану и разбирать готовые детали.
Машина для нестинга внешне очень похожа на продвинутый фрезер с ЧПУ: портальное исполнение, вакуумный рабочий стол большого формата, автосмена инструмента. Однако, у станка есть и дополнительное оснащение, которое очень серьезно повышает его автономность. С помощью присосок он самостоятельно берет лист из стопки и укладывает на рабочий стол. После раскроя станок специальным толкателем сдвигает заготовки со стола (заодно пылесосит стол от опилок), и этим тоже экономит массу времени. А присадочная голова сверлит отверстия под фурнитуру в несколько раз быстрее, чем фрезер, вооруженный, например, фрезой 4 мм.
«Быстрее всего центр справляется с «чистым» раскроем листа, на это уходит 3-5 минут, — рассказывает руководитель направления «Обрабатывающие центры с ЧПУ» Максим Шелихов. — Если мы добавляем присадку отверстий, время обработки увеличивается в два раза. Особенно много времени уходит на производство фасадов, там каждая дополнительная обработка фрезами добавляет те же 5-7 минут. Когда мы делали на выставке сложные фасады c применением 9 фрез в одной карте, обработка длилось более часа». Стоит отметить, что максимальная эффективность нестинга не достигается по причинам, которые можно назвать культурологическими. Оригинальная технология настроена на использование специальной фурнитуры, которую ставят только в пласть, но реальность вносит коррективы. «У нас в России,— поясняет Максим Шелихов, — люди не верят в мебель без шкантов. Не верят и не покупают, даже если вы используете навороченную фурнитуру. Могу прямо сказать, что это специфика нашего рынка, мы никак не можем уйти от торцевой присадки. Раньше мы предлагали в дополнение к нестингу специальный станок с ЧПУ, который сверлит только торцы, но им не особенно заинтересовались, люди предпочитают стандартные сверлильно-присадочные станки с ЧПУ. |
![]() |
С другой стороны, если бы мы работали за рубежом, купили нестинг и захотели увеличить производительность, то сразу уперлись бы в возможности оборудования. Нам осталось бы только покупать новые станки. А наши мебельщики пошли другим путем: нестинги используют только для раскроя (т.е. повышают производительность), а рядом ставят присадку с ЧПУ, которая сверлит и торцы и пласть. Один сверлильно-присадочный станок по производительности как раз соответствует нестингу.
Это общемировая статистика: один нестинг, одна присадка с ЧПУ с одной головой и два кромочника. В Китае эта схема очень часто встречается даже на крупных предприятиях.
Если взять сверлилку с тремя головами, две сверху и одна снизу, то она потянет, я думаю, два нестинга. Единственный момент, что нестинги будут работать 8 часов, а присадка около 10, но зато получим уже вполне солидный объем. На практике, на одном обрабатывающем центре стабильно делают около 30 кухонь в месяц».
Почему мы вообще сравниваем пильные и обрабатывающие центры? Потому что эпоха крупных серий уходит в прошлое, мебельный рынок постепенно дрейфует в сторону широких ассортиментов и маленьких партий.
Современные компании, особенно те, что снабжают интернет-магазины, стремятся работать так: получили заказ — сформировали карту раскроя и отправили на производство — напилили, закромили, присадили, отгрузили. Все максимально быстро, «утром деньги — вечером стулья». А значит, нет времени собирать заказы в пачку, и станки обрабатывают по одному листу. Посмотрим, насколько эффективно они это делают.
«Я исхожу из опыта производств, о которых знаю. — говорит Константин Червяков. — Рекордных результатов достигла воронежская фабрика, которая занимается как раз коммерческим раскроем. За 12 часов ребята снимают с раскроечного центра 120 листов. Скорее всего, они там работают очень интенсивно, без обеда и перекура, но этот объем реально сделать, работая по одному листу».
«Если говорить только про раскрой,— уточняет Максим Шелихов, — то на станке с автоматической выгрузкой за смену мы успеем обработать около 80 листов. С присадкой уже 40, а если будем фрезеровать фасады, обрабатывать столешницы, искусственный камень и HPL–пластик, то еще меньше. Но на пильном центре этого не сделать вообще.
К слову, обычный фрезер с ЧПУ за смену раскраивает примерно 20–25 листов, потому что много времени занимает уборка деталей со стола. Пока станок работал, оператор сидел и ждал, а потом они поменялись. И станок простаивает столько же, сколько обрабатывал лист, а то и больше.
Автоматическая выгрузка максимально увеличивает машинное время. Мы столкнули детали, запустили новый лист в обработку, а в это время оператор спокойно наклеивает этикетки и убирает раскрой. На всех наших центрах по умолчанию есть механизм разгрузки (он же очистка стола), так же, как и загрузочные присоски».
Сравним цены. По словам экспертов LIGA, самый доступный форматно-раскроечный центр стоит примерно 51 тысячу долларов, а обрабатывающий центр — 55 тысяч. Но средняя комплектация пильного центра обойдется уже примерно в 60–70 тысяч долларов.
Пильный центр выигрывает в цене инструмента и в себестоимости раскроя: 5 рублей за лист против 60 рублей у обрабатывающего центра. Однако, нестинг оптимизирует раскладку деталей на листе.
«Да, ширина пилы 4 мм, а диаметр фрезы 12 мм, — комментирует Максим Шелихов, — но мало кто вспоминает, что в нестинге принципиально другая раскладка деталей, которая экономит материал. При обычном раскрое мы привязываемся к прямым пропилам: сначала делаем головной рез, который формует лист в размер, потом пилим полосы, а потом эти полосы пилим на детали.
В нестинге мы раскладываем детали так, как хотим, поэтому в 80% случаев на лист для нестинга ложится больше деталей, чем на лист для раскроя. В остальных случаях — поровну».
Нельзя обойти стороной и оснащение станков, потому что при прочих равных выиграет тот, у кого лучше инструмент. Но здесь тоже паритет, потому что компания LIGA снабжает своих клиентов одинаково качественными пилами и фрезами.
«Высокоскоростной раскрой плитных материалов — абсолютный тренд мебельной промышленности, — говорит директор департамента Комплексного Снабжения Александр Есипов. — На сегодняшний день для наших партнеров крайне важна максимальная производительность используемого оборудования. Именно поэтому недавно мы продемонстрировали в работе алмазную фрезу SURREY серии Diamond Expert ф12 мм с разнесенной конфигурацией режущих зубьев, позволяющей производить раскрой ЛДСП на скорости подачи до 25 м/мин, и самую современную конфигурацию промышленных дисковых пил Golden Eagle Extremal ф400 мм, обеспечивающей возможность пакетного раскроя на скорости до 100 м/мин». Другими словами, диапазон разбега в обрабатываемых листах, в зависимости от технологии, может составлять до 80 листов раскроя в смену. Если нужно пилить больше и дешевле (и по одним картам), то добро пожаловать в царство пильных центров. Если больше не надо, а на картах раскроя есть криволинейные детали, то вас ждут обрабатывающие центры с ЧПУ для нестинга. Кроме того, есть и чисто организационные моменты, с которыми вторые справляются лучше. |
![]() |
«Нестинг проще масштабировать, — признает Константин Червяков. — Мы периодически посещаем китайские производства, которые как раз производят индивидуальную мебель в больших объемах и стараются максимально все автоматизировать. Так вот, они ставят несколько нестингов в ряд, и каждый из них режет свою карту раскроя. И далее стоит роботизированная система, которая передает детали на следующие участки. Люди нужны только для того, чтобы контролировать работу систем.
А на разгрузке раскроечного центра чаще всего стоит человек, пока нет автоматизации данного участка того же уровня, как на нестинге. Я не видел реализованных проектов с роботом-манипулятором, все остается на уровне концепта».
![]() |
Владимир Клименченко, торгово-производственная компания «Отличник», г. Краснодар: «У нас два направления: серийная мебель, детская и школьная, и премиальная мебель по дизайн-проектам. Перерабатываем около тысячи листов в месяц, примерно, 40–60 листов за смену. Начинали мы с премиального форматного станка, это был Altendorf в топовой комплектации. Но, во-первых, в серийной детской мебели был большой процент криволинейных деталей, во-вторых, нам нужно было фрезеровать сложные фасады. И, чтобы уйти от шаблонов и ручного труда, мы взяли нестинг с присадочной головой KDT KN-3710D (хотя обычно работает сверлильно-присадочный станок с ЧПУ KDT KD-612KHZ). А потом, чтобы еще ускориться, взяли пильный центр в серьезной комплектации KDT KS-832H. |
Если в двух словах, то «пильник» хорош для серии, а на индивидуальных заказах он не нужен от слова «вообще». Нестинг лучше подходит для раскроя «криволинейки», фасадов и т. д. Он делает фрезеровки под разные задачи, от подсветки до фурнитуры. А если требования к кромке предъявляют не очень высокие, то можно даже использовать кромочник без прифуговки, край довольно ровный. Лист пилится примерно 7-10 минут, для заказной мебели этого более чем достаточно.
На что обращать внимание при выборе? Сначала надо понять, что вы будете делать. Для нестинга шпиндель должен быть мощным, не какие-нибудь 6,5 кВт, а 9 или вообще 11-13 кВт. Но если берете станок для производства фасадов, тогда мощность шпинделя, наоборот, можно сделать поменьше, чтобы не платить за лишние киловатты. У многих на фасадах стоят недорогие фрезерные станки с ЧПУ и прекрасно работают.
Если вы берете станок такого уровня как нестинг или пильный центр, чтобы поиграться, — это так себе идея. Они хороши тем, что их можно интегрировать в производственную линию. Например, ТЗ от технолога сразу идет на станок, а тот кроит детали и клеит бирку. На ней есть наименование заказа, детали, размеры, указание, где и как кромить — этой информации достаточно, чтобы люди не гадали, что за деталь, и что с ней делать.
Когда мы приобретали станок, автоматическое нанесение было экзотикой, причем дорогой, поэтому у нас бирку оператор наклеивает руками. Но это не проблема, пока идет распил, у оператора есть время и на бирки, и на детали.
Что сказать по инструменту? На мой взгляд, нет смысла покупать дешевый инструмент, но тут каждому свое. Мы покупаем нормальный алмазный инструмент, берем не просто цанговые, а гидропатроны, у них меньше биение и инструмент работает надежнее, стабильнее.
Мы брали и Leuco, и Leitz и Surrey, и не было такого, чтобы какие-то фрезы ходили 100 листов, а другие 300. Разброс большой, примерно от 180 до 250, но, в среднем, фрезы у нас ходят больше 200 листов».
Игорь Карась, мебельная фабрика «Кариви», г. Королев: «Мы производим много разной детской мебели. Трудно угадать, что выберет покупатель, поэтому мы просто берем и делаем очень много разных моделей. Технология нестинга позволяет быстро менять задачу производству. В основном используем ЛДСП 16 мм от «Увадрев», Lamarty, Kronospan. За 8-часовую смену пилим 110–120 листов на трех нестингах KDT KN-3710D. Они у меня работают одновременно, но абсолютно вразнобой. Нестинг сталкивает детали на разгрузочный стол, и со стола оператор их разбирает, пока следующий лист уже в работе. По лазерной метке и целеуказанию оператор четко, без размышлений клеит этикетки с невероятной скоростью. Когда специальный лазерный проектор показывает, в каком направлении двигаться, это получается быстро. |
![]() |
Зачем лазерные метки? Чтобы избежать влияния человеческого фактора. Оператор клеит этикетки каждые 7 минут, глаз у него замыливается, он может повернуть их не той стороной. И все. Дальше деталь либо закромят не с той стороны, либо присадочник затупит, потому что деталь не проходит, либо вообще сверло сломает. К слову, мы уже делаем автоматическое этикетирование.
Идет конвейер, и на него постоянно поступают детали. Их отправляют на присадочные станки (два KDT KD-612MHS), потом на кромочные станки (два KDT KE-665JSKA). Потом детали складывают на специальный стеллаж, а уже стеллаж сам показывает сборщику, что именно надо брать. Да, и упаковка тоже работает через сканирование штрих-кодов. Не знаю, правильная ли это организация производства, я не мебельщик. Но в день мы отгружаем 300 больших коробок, это где-то 7 тонн мебели в день.
Я продавал детскую мебель, и в определенный момент поставщики начали мне выкручивать руки и нарушать договоренности. Я сказал, что построю свой Лунапарк с блэкджеком, и построил его за год, не такой, как у других.
Когда я смотрел на чужие производства, то не понимал, как у них получается делать мебель. По-моему, человеку нереально сделать, условно, тысячу резов и ни разу не ошибиться при выставлении размеров. А потом хлоп, и вся партия шкафов перестает собираться. Поэтому мне хотелось, чтобы мебельное производство было максимально автоматизировано.
Основная идея, что люди не должны ничего носить, все должно делаться само. Да, пока что людей, перекладывающих детали со станка на станок, нечем заменить, но мы движемся в этом направлении. Вообще, у меня в планах, чтобы все делали роботы. Пока что это биороботы, работающие на этаноле, но когда-нибудь я поставлю механических.
Почему я выбрал KDT? По соотношению цены и основной комплектации. Вначале я брал разную «солянку», тогда это было тестовое производство, просто чтобы получить от оборудования максимальные результаты. С этой точки зрения, конечно, китайцы дают гораздо больше за те же деньги. А потом я избавился от тех китайцев, которые попроще, и поставил более наполненные станки.
KDT мне понравились, присадочники у них вообще великолепные, как и нестинги. Самый первый станок, которому сейчас 4 с небольшим года, прекрасно работает, так же, как и самый новый из них, которому год. За это время на нем поменяли поддерживающий цилиндр за пять тысяч рублей, мне не понравилось, что он начал шуметь. И все. Они у меня работают по 8 часов непрерывно 6 дней в неделю».
* * *Чтобы определиться в пользу пильного или обрабатывающего центра, мебельщик должен понимать сильные и слабые стороны технологий. Их объединяет то, что оба вида оборудования уменьшают влияние человеческого фактора и повышают качество раскроя.
Пильные центры имеют преимущества в серийном производстве, где карты раскроя повторяются и можно пилить ЛДСП пакетом, по 2-5-7 листов. Кроме того, это оборудование предпочитают фабрики, оказывающие услуги коммерческого раскроя.
Обрабатывающие центры с ЧПУ для нестинга несколько отличаются от своих собратьев, 3D-фрезеров. У них есть дополнительное оснащение, расширяющее возможности: механизм захвата листа и укладки на рабочий стол, позиционеры, присадочная голова и т. д. За счет этого, они могут работать в непрерывном режиме, без участия оператора. То есть, нестинг проще встроить в автоматизированный производственный процесс.
Если предприятие перерабатывает до 80 листов в смену, то ему логичнее сделать выбор в пользу гибкого решения — обрабатывающего центра.
За подробностями обращайтесь к экспертам компании LIGA:
- руководитель направления «Раскроечное оборудование» Константин Червяков: ckv@ligamachinery.com +7 926 429 6532
- руководитель направления «Обрабатывающие центры с ЧПУ» Максим Шелихов: shelihov.m@ligamac.com +7 926 436 49 68